The Basic Terms
The Origin of Oil and Gas
Conditions for Oil and Gas Formation
Occurrence of Oil and Gas - four conditions
Types of Oil Traps
oil dome photo
oil dome section
fault trap
sand lens
salt dome
unconformity trap
see also Oil Deposits - types of traps (different file)
see also Bio Fuels Fuels Oil and Gas Exploration Offshore Oil and Gas Refining Oil Spills
The Basic Terms
Petroleum
- A broad term which includes both crude oil and natural gas
Crude Oil
- a liquid mixture of naturally occurring hydrocarbons (compounds containing carbon and oxygen).
Natural Gas
- A gaseous mixture of naturally occurring hydrocarbons.
The Origin of Oil and Gas
Oil and natural gas originate from organic matter in marine sediment. Microscopic organisms such as single-celled algae settle to the sea floor and accumulate in marine mud. This organic matter may partially decompose, using up the dissolved oxygen in the sediment. As soon as the oxygen is used up, decay stops and the remaining organic matter is preserved. Continued burial subjects the organic matter to higher temperatures and pressures, which cause physical and chemical changes in the organic compounds. These changes produce tiny droplets of oil and natural gas. As muddy sediments compact, the oil and gas are squeezed out and move into more porous and permeable sandy layers.
Conditions for Oil and Gas Formation
Anaerobic
- conditions under which oxygen is not present. This is the condition necessary for the formation of oil and gas. Such conditions are found in a highly restrictive environment such as in a closed basin like the bottom of the Black Sea.
Aerobic
- conditions under which oxygen is present to oxidize organic material and sulfur.
Occurrence of Oil and Gas
Four conditions or requirements are necessary in order for large accumulations of oil and gas to form. The requirements are:
Source Rock
- A shale must contain organic material which has not been oxidized and which is converted to petroleum by burial pressures and temperatures.
Reservoir Rock
- A sandstone or other relatively porous rock is required to store and transmit the petroleum when wells are drilled into the reservoir.
A Trap
- a set of conditions to hold the petroleum in a reservoir and prevent its escape by migration.
Deep enough burial but not too deep - Temperatures and Pressures are required to "cook" the petroleum out of the organic matter. Of course, if the rock gets too hot the petroleum is all "burned" off.
Types of traps:
Oil Dome

Oil Dome in section

Fault Trap

Sand Lens

Salt Dome

Unconformity Trap

http://earthsci.org/mineral/energy/gasexpl/offshore.html
Offshore Oil Drilling
adapted to HTML from Australian Institute of Petroleum with permission Offshore Exploration Oil Spills Refining Oil
Drilling or digging for oil has occurred in one way or another for hundreds of years. The Chinese, for instance, invented a bamboo rig to obtain oil and gas for lighting and cooking.

In Australia, nearly 90 per cent of our petroleum wealth is found offshore. The search is difficult, extremely expensive, and often fruitless - but critical to the nation's economic future.
Locating an oil and gas "trap" - as it is known - and extracting the oil and gas is difficult enough on land. But offshore, in deep and often stormy waters, it becomes an awesome undertaking.
Potential traps are identified by analysing seismic survey data but whether they contain oil or gas won't be known until a drill bit penetrates the structure. Directing the drill bit to a precise location - perhaps several kilometres away - requires sophisticated computer technology. A navigation device installed above the drill bit feeds back information which enables the exact position of the well to be measured and monitored. A steerable motor within the drillpipe can be remotely controlled to adjust the direction of the drill.
![]() | ![]() | |
Anticlinal Trap | Fault Trap |

Environmental safeguards
The Australian offshore petroleum industry has always contended that its activities are environmentally friendly.
The industry's case has now been given increased strength with the findings of the Independent Scientific Review Committee (ISRC) inquiry commissioned by the Australian Petroleum Exploration Association.
In Australia up to 100 offshore wells per year are drilled. About a quarter of these are development wells to produce oil or gas found by previous drilling.
Before a well can be drilled, government approval must be obtained. Drilling must then conform to statutory conditions and further operations are covered by industry Codes of Practice.
The Independent Scientific Review has found that environmental impacts from offshore exploration and production are negligible. The ISR examined the potential environmental effects of discharge of drilling fluids, drill cuttings and "produced formation water" (PFW).
Companies in Australia safeguard the environment and minimise impacts in a number of ways.
Drilling fluids used in Australia are almost exclusively water-based, not oil-based.
During production, oil is separated from the water by mechanical devices before the produced formation water is returned to sea. Australia's regulations on how much petroleum hydrocarbon is contained in PFW are among the world's strictest.
Sophisticated and reliable blowout prevention systems (BOP) are used in every production well to minimise the possibility of a blowout - where uncontrolled fluids flow from a well.
Four drilling rig types
In the early days of offshore drilling, explorers simply fitted a derrick to a barge and towed it to their site. Today, four types of offshore rigs are used to drill wildcat or exploration wells.
Submersibles. These are rarely used. They can be floated to shallow water locations then ballasted to sit on the seabed. Jackups. Usually towed to a location. Their legs are then lowered to the seabed and the hull is jacked-up clear of the sea surface. Used in waters to about 160 metres deep.Production platforms Once oil or gas is discovered, the drilling rig is generally replaced by a production platform, assembled at the site using a barge equipped with heavy lift cranes.
Drill ship. These look like ordinary ships but have a derrick on top which drills through a hole in the hull. Drill ships are either anchored or positioned with computer-controlled propellers along the hull which continually correct the ships drift. Often used to drill "wildcat" wells in deep waters.
Semi submersible. Mobile structures, some with their own locomotion. Their superstructures are supported by columns sitting on hulls or pontoons which are ballasted below the water surface. They provide excellent stability in rough, deep seas.
Platforms vary in size, shape and type depending on the size of the field, the water depth and the distance from shore. In Australia's medium to large fields, fixed production platforms are commonly used.
These are made of steel and fixed to the seabed with steel piles. These platforms house all the processing equipment and accommodate up to 80 workers who typically work a 12 hour day, one week on and one week off. There are also concrete structures which are big enough to store oil. Gravity holds them on the seabed.
The world's biggest platforms are bigger than a football field and rise above the water as high as a 25 storey office tower. They are home to 500 workers.
If the field is in shallow water and near land or another platform, small remotely controlled monopod platforms may be used. Another system is a floating structure, either anchored or tethered, called a Floating Production Storage Offloading (FPSO) vessel.
Another platform type, suitable for deep water production, is the Tension Leg platform, built of steel or concrete and anchored to the sea floor with vertical "tendons".
Drilling for oil
The first stage of drilling is called "spudding" and drilling starts when the drill bit is lowered into the seabed.
The bit can be of two types: - a roller cone or rock bit which usually has three cones armed with steel or tungsten carbide : teeth:; or buttons; or - a diamond bit, imbedded with small industrial diamonds.
The drill bit is attached to drill pipe (or a drill string) and rotated by a turntable on the platform floor. As the hole deepens, extra lengths of drill pipe are attached.
A length of drill pipe is 30 feet long, or 9.1 metres (oil workers use the old imperial measurement system). The drill bit ranges in diameter from 36 inches or approximately 91.4 centimetres (used at the start of the hole) to eight and a half inches (approximately 21.5 centimetres).
Drilling may take weeks or months before the targeted location is reached.
The major potential environmental effects from offshore drilling result from the discharge of wastes, including drilling fluids, drill cuttings and "produced formation water" (PFW).
Drilling fluid
Drilling fluid is pumped down the drill pipe and into the hole at high velocity through nozzles in the drill bit. The fluid is usually a mixture of water, clay, a weighting material (usually barite), and various chemicals.
The drilling fluid serves several purposes. It raises the drill cutting to the surface for disposal; it provides the "weight" to keep the underground pressures in check; it keeps the hold stable by caking the wall with a thin layer of clay; and it cleans and cools the bit.
The fluid is recycled through a circulation system where equipment mounted on the drilling rig separates out the drill cuttings and allows the clean fluid to be pumped back down the hole. With few exceptions, Australian wells since 1985 have been drilled using water-based drilling fluids, not oil-based.
The ISRC concluded that "drilling waste discharges have generally been shown to have only minor effects on water quality and pelagic ecosystems".
Evidence collected by the ISRC suggests that acute toxic effects of drilling fluids on marine organisms are only found at very high concentrations. "Toxic effects on the biota in the water column from such concentrations would only be present within a few tens of metres from the point of discharge and only for short times after discharge".
As the plume of drilling fluid and cuttings falls to the seabed, it disperses, with 90 percent of it settling within 100 metres of the platform. Soluble waste concentrations will have fallen by a factor of 10,000 within 100 metres and suspended sediment concentrations by a factor of at least 50,000.
Drill cuttings
As the well is drilled, the "cuttings", consisted of crushed rock and clay, are brought to the surface by the drilling fluid and discharged overboard.
New measures to reduce discharges such as re-injecting the cuttings into the well and slim hole drilling are being examined and tested by the industry.
Produced formation water
Where you find oil, you often also find water. As oil is drawn from a reservoir, it is therefore necessary to separate the water and return it to the ocean.
This is what is known as "produced formation water" (PFW). Great emphasis is placed on ensuring that the water returned to the ocean is as free as possible from oil and chemicals. Strict regulations apply on how much petroleum hydrocarbon is contained in PFW. The Australian regulatory limit is 30 mg/litre average. Mechanical separation devices and chemical treatments are used to separate oil and water efficiently.
Preventing "blow-outs"
The weight of the drilling fluid acts as the first line of well control by keeping underground pressures in check. If an influx of pressurised oil or gas does occur during drilling, well control is maintained through the rig's blowout prevention system (BOP). This is a set of hydraulically operated valves and other closure devices (rams) which seal off the well, and route the wellbore fluids to specialised pressure controlling equipment.
Trained personnel operating this highly reliable equipment minimise the possibility of a "blowout", or an uncontrolled flow of fluids from a well.
Directional drilling
Drilling an oil well may not be a case of going straight down. Directional drilling has been developed where drill bits are steered laterally over a distance of up to several kilometres towards the petroleum reservoir.
One production platform is often used to drill a number of wells, in a variety of directions and inclinations. To steer the drill bit, a downhole motor may be used. It is turned by pumping the drilling mud through it.
Completing the well
When the well has been drilled to its target depth, production casing is set and cemented.
Tubing is lowered into the hole together with "packers" which seal the space between the tubing and the casing. Finally, at the end of the well, the casing is perforated at predetermined depths by small explosive charges detonated remotely. The small holes in the casing allow the oil or gas under its natural pressure to flow to the surface.
A dry well
If the drilled hole is considered to be "dry" or not worth developing, the decision is made to "plug and abandon" it. This involves setting several cement plugs in the well.
Refining of Petroleum
adapted to HTML from Australian Institute of Petroleum with permission Offshore Exploration Offshore Drilling Oil Spills
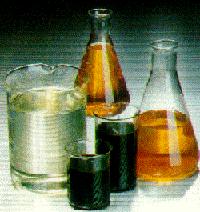
An oil refinery is an organised and coordinated arrangement of manufacturing processes designed to produce physical and chemical changes in crude oil to convert it into everyday products like petrol, diesel, lubricating oil, fuel oil and bitumen.
As crude oil comes from the well it contains a mixture of hydrocarbon compounds and relatively small quantities of other materials such as oxygen, nitrogen, sulphur, salt and water. In the refinery, most of these non - hydrocarbon substances are removed and the oil is broken down into its various components, and blended into useful products.
Natural gas from the well, while principally methane, contains quantities of other hydrocarbons - ethane, propane, butane, pentane and also carbon dioxide and water. These components are separated from the methane at a gas fractionation plant.
Petroleum hydrocarbon structures
Petroleum consists of three main hydrocarbon groups:
Paraffins
- These consist of straight or branched carbon rings saturated with hydrogen atoms, the simplest of which is methane ( CH 4) the main ingredient of natural gas. Others in this group include ethane ( C 2 H 6), and propane ( C 3 H 8).
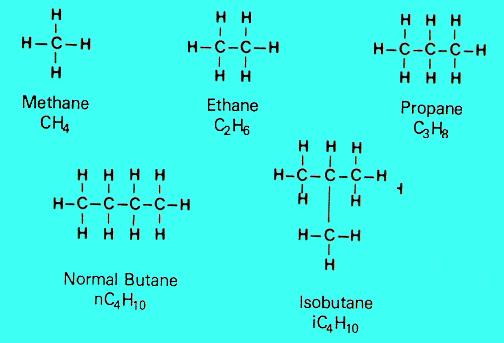
- With very few carbon atoms ( C 1to C 4) are light in density and are gases under normal atmospheric pressure. Chemically paraffins are very stable compounds.
- Naphthenes consist of carbon rings, sometimes with side chains, saturated with hydrogen atoms. Naphthenes are chemically stable, they occur naturally in crude oil and have properties similar to paraffins.

- aromatic hydrocarbons are compounds that contain a ring of six carbon atoms with alternating double and single bonds and six attached hydrogen atoms. This type of structure is known as a benzene ring. They occur naturally in crude oil, and can also be created by the refining process.
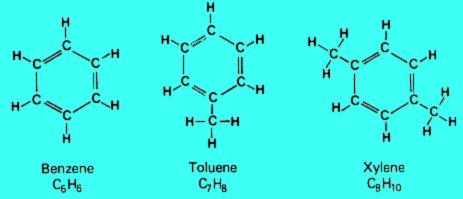
Small quantities of a crude oil may be composed of compounds containing oxygen, nitrogen, sulphur and metals. Sulphur content ranges from traces to more than 5 per cent. If a crude oil contains appreciable quantities of sulphur it is called a sour crude; if it contains little or no sulphur it is called a sweet crude.
The refining process
Every refinery begins with the separation of crude oil into different fractions by distillation.

The fractions are further treated to convert them into mixtures of more useful saleable products by various methods such as cracking, reforming, alkylation, polymerisation and isomerisation. These mixtures of new compounds are then separated using methods such as fractionation and solvent extraction. Impurities are removed by various methods, e.g. dehydration, desalting, sulphur removal and hydrotreating.
Refinery processes have developed in response to changing market demands for certain products. With the advent of the internal combustion engine the main task of refineries became the production of petrol. The quantities of petrol available from distillation alone was insufficient to satisfy consumer demand. Refineries began to look for ways to produce more and better quality petrol. Two types of processes have been developed:
- breaking down large, heavy hydrocarbon molecules
- reshaping or rebuilding hydrocarbon molecules.
Atmospheric distillation takes place in a distilling column at or near atmospheric pressure. The crude oil is heated to 350 - 400 o C and the vapour and liquid are piped into the distilling column. The liquid falls to the bottom and the vapour rises, passing through a series of perforated trays (sieve trays). Heavier hydrocarbons condense more quickly and settle on lower trays and lighter hydrocarbons remain as a vapour longer and condense on higher trays.
Liquid fractions are drawn from the trays and removed. In this way the light gases, methane, ethane, propane and butane pass out the top of the column, petrol is formed in the top trays, kerosene and gas oils in the middle, and fuel oils at the bottom. Residue drawn of the bottom may be burned as fuel, processed into lubricating oils, waxes and bitumen or used as feedstock for cracking units.
To recover additional heavy distillates from this residue, it may be piped to a second distillation column where the process is repeated under vacuum, called vacuum distillation. This allows heavy hydrocarbons with boiling points of 450 o C and higher to be separated without them partly cracking into unwanted products such as coke and gas.
The heavy distillates recovered by vacuum distillation can be converted into lubricating oils by a variety of processes. The most common of these is called solvent extraction. In one version of this process the heavy distillate is washed with a liquid which does not dissolve in it but which dissolves (and so extracts) the non-lubricating oil components out of it. Another version uses a liquid which does not dissolve in it but which causes the non-lubricating oil components to precipitate (as an extract) from it. Other processes exist which remove impurities by adsorption onto a highly porous solid or which remove any waxes that may be present by causing them to crystallise and precipitate out.

Reforming
Reforming is a process which uses heat, pressure and a catalyst (usually containing platinum) to bring about chemical reactions which upgrade naphthas into high octane petrol and petrochemical feedstock. The naphthas are hydrocarbon mixtures containing many paraffins and naphthenes. In Australia, this naphtha feedstock comes from the crudes oil distillation or catalytic cracking processes, but overseas it also comes from thermal cracking and hydrocracking processes. Reforming converts a portion of these compounds to isoparaffins and aromatics, which are used to blend higher octane petrol.
- paraffins are converted to isoparaffins
- paraffins are converted to naphthenes
- naphthenes are converted to aromatics
catalyst | ||||||
---|---|---|---|---|---|---|
heptane | -> | toluene | + | hydrogen | ||
C 7 H 16 | -> | C 7 H 8 | + | 4H 2 |
catalyst | ||||||
---|---|---|---|---|---|---|
cyclohexane | -> | benzene | + | hydrogen | ||
C 6 H 12 | -> | C 6 H 6 | + | 3H 2 |
Cracking processes break down heavier hydrocarbon molecules (high boiling point oils) into lighter products such as petrol and diesel. These processes include catalytic cracking, thermal cracking and hydrocracking.
e.g.
A typical reaction:
catalyst | ||||||
---|---|---|---|---|---|---|
C 16 H 34 | -> | C 8 H 18 | + | C 8 H 16 |
Catalytic cracking is used to convert heavy hydrocarbon fractions obtained by vacuum distillation into a mixture of more useful products such as petrol and light fuel oil. In this process, the feedstock undergoes a chemical breakdown, under controlled heat ( 450 - 500 o C ) and pressure, in the presence of a catalyst - a substance which promotes the reaction without itself being chemically changed. Small pellets of silica - alumina or silica - magnesia have proved to be the most effective catalysts.
The cracking reaction yields petrol, LPG, unsaturated olefin compounds, cracked gas oils, a liquid residue called cycle oil, light gases and a solid coke residue. Cycle oil is recycled to cause further breakdown and the coke, which forms a layer on the catalyst, is removed by burning. The other products are passed through a fractionator to be separated and separately processed.
Fluid catalytic cracking uses a catalyst in the form of a very fine powder which flows like a liquid when agitated by steam, air or vapour. Feedstock entering the process immediately meets a stream of very hot catalyst and vaporises. The resulting vapours keep the catalyst fluidised as it passes into the reactor, where the cracking takes place and where it is fluidised by the hydrocarbon vapour. The catalyst next passes to a steam stripping section where most of the volatile hydrocarbons are removed. It then passes to a regenerator vessel where it is fluidised by a mixture of air and the products of combustion which are produced as the coke on the catalyst is burnt off. The catalyst then flows back to the reactor. The catalyst thus undergoes a continuous circulation between the reactor, stripper and regenerator sections.
The catalyst is usually a mixture of aluminium oxide and silica. Most recently, the introduction of synthetic zeolite catalysts has allowed much shorter reaction times and improved yields and octane numbers of the cracked gasolines.
Thermal cracking uses heat to break down the residue from vacuum distillation. The lighter elements produced from this process can be made into distillate fuels and petrol. Cracked gases are converted to petrol blending components by alkylation or polymerisation. Naphtha is upgraded to high quality petrol by reforming. Gas oil can be used as diesel fuel or can be converted to petrol by hydrocracking. The heavy residue is converted into residual oil or coke which is used in the manufacture of electrodes, graphite and carbides.
This process is the oldest technology and is not used in Australia.
Hydrocracking can increase the yield of petrol components, as well as being used to produce light distillates. It produces no residues, only light oils. Hydrocracking is catalytic cracking in the presence of hydrogen. The extra hydrogen saturates, or hydrogenates, the chemical bonds of the cracked hydrocarbons and creates isomers with the desired characteristics. Hydrocracking is also a treating process, because the hydrogen combines with contaminants such as sulphur and nitrogen, allowing them to be removed.
Gas oil feed is mixed with hydrogen, heated, and sent to a reactor vessel with a fixed bed catalyst, where cracking and hydrogenation take place. Products are sent to a fractionator to be separated. The hydrogen is recycled. Residue from this reaction is mixed again with hydrogen, reheated, and sent to a second reactor for further cracking under higher temperatures and pressures.
In addition to cracked naphtha for making petrol, hydrocracking yields light gases useful for refinery fuel, or alkylation as well as components for high quality fuel oils, lube oils and petrochemical feedstocks.
Following the cracking processes it is necessary to build or rearrange some of the lighter hydrocarbon molecules into high quality petrol or jet fuel blending components or into petrochemicals. The former can be achieved by several chemical process such as alkylation and isomerisation.
Alkylation
Olefins such as propylene and butylene are produced by catalytic and thermal cracking. Alkylation refers to the chemical bonding of these light molecules with isobutane to form larger branched-chain molecules (isoparaffins) that make high octane petrol.
Olefins and isobutane are mixed with an acid catalyst and cooled. They react to form alkylate, plus some normal butane, isobutane and propane. The resulting liquid is neutralised and separated in a series of distillation columns. Isobutane is recycled as feed and butane and propane sold as liquid petroleum gas (LPG).
e.g.
catalyst | ||||||
---|---|---|---|---|---|---|
isobutane | + | butylene | -> | isooctane | ||
C 4 H 10 | + | C 4 H 8 | -> | C 8 H 18 |
Isomerisation
Isomerisation refers to chemical rearrangement of straight-chain hydrocarbons (paraffins), so that they contain branches attached to the main chain (isoparaffins). This is done for two reasons:
- they create extra isobutane feed for alkylation
- they improve the octane of straight run pentanes and hexanes and hence make them into better petrol blending components.
Polymerisation
Under pressure and temperature, over an acidic catalyst, light unsaturated hydrocarbon molecules react and combine with each other to form larger hydrocarbon molecules. Such process can be used to react butenes (olefin molecules with four carbon atoms) with iso-butane (branched paraffin molecules, or isoparaffins, with four carbon atoms) to obtain a high octane olefinic petrol blending component called polymer gasoline.
Hydrotreating and sulphur plants
A number of contaminants are found in crude oil. As the fractions travel through the refinery processing units, these impurities can damage the equipment, the catalysts and the quality of the products. There are also legal limits on the contents of some impurities, like sulphur, in products.
Hydrotreating is one way of removing many of the contaminants from many of the intermediate or final products. In the hydrotreating process, the entering feedstock is mixed with hydrogen and heated to 300 - 380 o C . The oil combined with the hydrogen then enters a reactor loaded with a catalyst which promotes several reactions:
- hydrogen combines with sulphur to form hydrogen sulphide ( H 2 S )
- nitrogen compounds are converted to ammonia
- any metals contained in the oil are deposited on the catalyst
- some of the olefins, aromatics or naphthenes become saturated with hydrogen to become paraffins and some cracking takes place, causing the creation of some methane, ethane, propane and butanes.
- the removal of the hydrogen sulphide gas from the hydrocarbon stream
- the conversion of hydrogen sulphide to elemental sulphur, a non-toxic and useful chemical.
- Combustion of part of the H 2 S stream in a furnace, producing sulphur dioxide ( SO 2) water ( H 2 O ) and sulphur (S).
- Reaction of the remainder of the H 2 S with the combustion products in the presence of a catalyst. The H 2 S reacts with the SO 2to form sulphur.
2H 2 S | + | 2O 2 | -> | SO 2 | + | S | + | 2H 2 O |
2H 2 S | + | 2O 2 | -> | 3S | + | 2H 2 O |
Air, water and land can all be affected by refinery operations. Refineries are well aware of their responsibility to the community and employ a variety of processes to safeguard the environment.
The processes described below are those used by the Shell refinery at Geelong in Victoria, but all refineries employ similar techniques in managing the environmental aspects of refining.
Air
Preserving air quality around a refinery involves controlling the following emissions:
- sulphur oxides
- hydrocarbon vapours
- smoke
- smells
Smoke is formed when the burning mixture contains insufficient oxygen or is not sufficiently mixed. Modern furnace control systems prevent this from happening during normal operation.
Smells are the most difficult emission to control and the easiest to detect. Refinery smells are generally associated with compounds containing sulphur, where even tiny losses are sufficient to cause a noticeable odour.
Water
Aqueous effluent's consist of cooling water, surface water and process water.
The majority of the water discharged from the refinery has been used for cooling the various process streams. The cooling water does not actually come into contact with the process material and so has very little contamination. The cooling water passes through large "interceptors" which separate any oil from minute leaks etc., prior to discharge. The cooling water system at Geelong Refinery is a once-through system with no recirculation.
Rainwater falling on the refinery site must be treated before discharge to ensure no oily material washed off process equipment leaves the refinery. This is done first by passing the water through smaller "plant oil catchers", which each treat rainwater from separate areas on the site, and then all the streams pass to large "interceptors" similar to those used for cooling water. The rainwater from the production areas is further treated in a Dissolved Air Flotation (DAF) unit. This unit cleans the water by using a flocculation agent to collect any remaining particles or oil droplets and floating the resulting flock to the surface with millions of tiny air bubbles. At the surface the flock is skimmed off and the clean water discharged.
Process water has actually come into contact with the process streams and so can contain significant contamination. This water is treated in the "sour water treater" where the contaminants (mostly ammonia and hydrogen sulphide) are removed and then recovered or destroyed in a downstream plant. The process water, when treated in this way, can be reused in parts of the refinery and discharged through the process area rainwater treatment system and the DAF unit.
Any treated process water that is not reused is discharged as Trade Waste to the sewerage system. This trade waste also includes the effluent from the refinery sewage treatment plant and a portion of treated water from the DAF unit.
As most refineries import and export many feed materials and products by ship, the refinery and harbour authorities are prepared for spillage from the ship or pier. In the event of such a spill, equipment is always on standby at the refinery and it is supported by the facilities of the Australian Marine Oil Spill Centre at Geelong, Victoria.
Land
The refinery safeguards the land environment by ensuring the appropriate disposal of all wastes.
Within the refinery, all hydrocarbon wastes are recycled through the refinery slops system. This system consists of a network of collection pipes and a series of dewatering tanks. The recovered hydrocarbon is reprocessed through the distillation units.
Wastes that cannot be reprocessed are either recycled to manufacturers (e.g. some spent catalysts can be reprocessed), disposed of in EPA-approved facilities off-site, or chemically treated on-site to form inert materials which can be disposed to land-fill within the refinery.
Waste movements within the refinery require a "Process liquid, Sludge and Solid waste disposal permit". Wastes that go off-site must have an EPA "Waste Transport Permit".
http://earthsci.org/mineral/energy/gasexpl/spill.html
Oil Spills
adapted to HTML from Australian Institute of Petroleum with permission Offshore Exploration Refining Oil Offshore Drilling
Oil spill prevention
Oil spill combat
Combat Techniques
How Dispersants work
The petroleum industry's safety record of handling oil and its products in Australia has been excellent and has been maintained throughout the last two decades of rapidly increasing volumes produced and transported in national waters. Oil spills from offshore production have been insignificant and, while there have been some spills arising from shipping accidents, none has had a lasting adverse impact on the marine environment.
The risks and responsibilities associated with oil in the sea should be put in their true perspective.
Only 14 per cent of the oil in the sea is directly attributable to the world's oil industry. Two per cent of this occurs in spills during the exploration and production phase from rigs and platforms, and 12 per cent is attributable to accidents involving oil tankers.
Another 33 per cent occurs during the operation of vessels other than those used by the oil industry. Usually these are cargo vessels which may be involved in collisions which spill fuel oil or they may discharge waste oil from ballast tanks during a voyage.

Major inputs of petroleum
to the marine environment
Oil spill prevention
Although statistics show that historically the oil industry is directly responsible for only a small proportion of marine oil spills, the oil companies - individually and collectively - do not take the risk of spills lightly. There are strict regulations governing all facets of their operations from the exploration / production phase through to the delivery of refined petroleum products.
Exploration & production: Almost 1,100 wells have been drilled and approximately 3,100 million barrels of oil have been produced in coastal and offshore Australia. Only about 600 barrels have been spilt in the marine environment from exploration and production operations. This is equivalent to the volume contained in a garden swimming pool and taken over a period of 25 years.
Above the water line, special deck drains on each rig and platform collect any waste fluids and channel them into settling tanks where oil is separated out, put into containers and sent to shore for treatment and disposal.
The Australian petroleum industry is a world leader in the treatment of water produced with oil through production wells offshore. Innovative technology includes the use of hydrcyclones and air stripping techniques to ensure the hydrocarbon content of formation water discharged into the sea is well under the Government regulatory limit of 30 parts per million.
The integrity of oil tankers is more difficult to control because the business of tanker operations is complex and fragmented. Oil company-owned vessels make up only about 15 per cent of the world fleet. Oil company-chartered tankers add another 20 per cent.
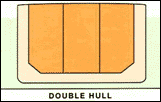
Oil spill combat
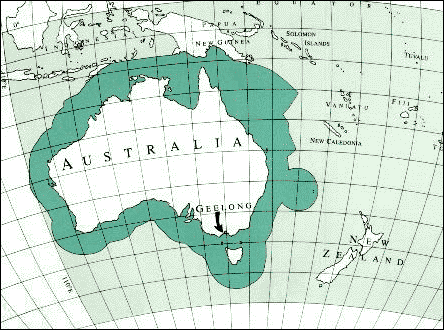
Australian Marine Oil Spill Centre Ltd (AMOSC): is wholly owned subsidiary of Australian Institute of Petroleum Ltd and is totally managed and funded by the Australian oil industry. There are eleven participating oil companies: Australian Petroleum Pty Limited, BHP Petroleum Pty Ltd, BP Australia Ltd, Esso Australia Ltd, Hadson energy Ltd, Mobil Oil, Australia Ltd, Santos Ltd, The Shell Company of Australia Ltd and Woodside Petroleum Ltd.
The Centre was established in 1990 to provide the equipment and trained personnel required to respond to a major oil spill off Australia's coasts. Based on Corio Bay, near Geelong in Victoria, it houses over $10 million of oil spill combat equipment and materials. This gear and the trained staff are on call 24 hours a day and they can be at the scene of a spill anywhere off Australia's coasts within 12-24 hours of being called out.
If additional back-up is needed AMOSC can call on international aid from a similar organisation based in Singapore (East Asia Response Ltd) as well as the world's largest spill organisation (Oil Spill Service Centre) located in Southampton, England. The latter has its own cargo plane on standby and can be at most locations within 48 hours of receiving a call.
AMOSC also has a purpose-built training centre where regular courses are held in oil response techniques. The Centre trains between 200 and 300 oil industry and government safety personnel each year. Marine Oil Spills Action Plan (MOSAP): was established by the oil industry in 1971 to enable an individual company to obtain assistance from other companies in combating a spill larger than it can handle with its own resources. Like AMOSC, MOSAP is supervised and funded by the oil industry through the Australian Institute of Petroleum.
The industry has provided equipment and clean-up materials at each port around Australia where oil is handled in bulk. A minor spill will be handled by the oil company concerned using the equipment available to it at or near the site. MOSAP is activated if a spill is beyond the capability of the company concerned.
If the spill is of major proportions, contact will be made with AMOSC and the Australian Maritime Safety Authority for assistance.
National Plan to Combat Pollution of the Sea by Oil (NATPLAN) has been in operation since October 1973. It is a combined effort by State and Federal organisations and the oil industry. Oil spill combat equipment is provided at various locations round Australia and a training program is conducted by the Australia Maritime Safety Authority. Funding for NATPLAN is based on the 'polluter pays' principle and a levy is placed on commercial shipping using Australian ports. These funds provide for the maintenance and administration of the Plan and allow for a contingency to cover costs not attributable to the polluter, or which the polluter is unable to meet.
Combat Techniques No two oil spills are the same because of the variation in oil types, locations and weather conditions involved. However, broadly speaking, there are four main methods of response.
- Leave the oil alone so that it breaks down by natural means.
- Contain the spill with booms and collect it from the water surface using skimmer equipment.
- Use dispersants to break up the oil and speed its natural biodegradation.
- Introduce biological agents to the spill to hasten biodegradation.
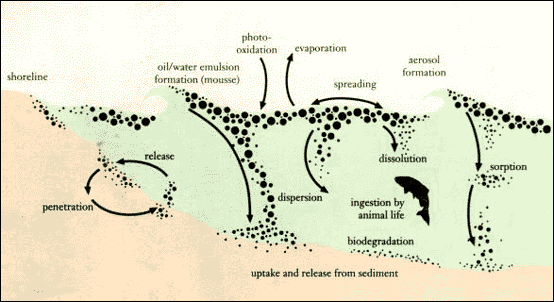
Processes Following a Spill
Often the response involves a combination of all these approaches.
Boom types vary from inflatable neoprene tubes to solid, but buoyant material. Most rise up about a metre above the water line. Some are designed to sit flush on tidal flats while others are applicable to deeper water and have skirts which hang down about a metre below the waterline.
Skimmers float across the top of the slick contained within the boom and suck or scoop the oil into storage tanks on nearby vessels or on the shore.
However booms and skimmers are less effective when deployed in high winds and high seas.
Decisions on whether or not to use dispersants to combat an oil spill must be made in each individual case. The decision will take into account the time since the spill, the weather conditions, the particular environment involved and the type of oil that has been spilt.
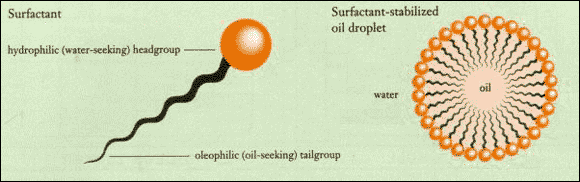
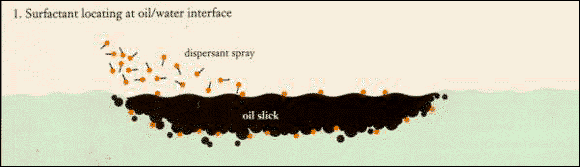
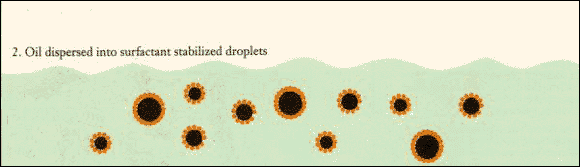
Bioremediation: Most of the components of oil washed up along a shoreline;can be broken down by bacteria and other micro-organisms into harmless substances such as fatty acids and carbon dioxide. This action is called bio-degradation. The addition of fertilising nutrients like nitrogen and phosphorous which stimulate growth of the micro-organisms concerned.
However the effectiveness of this technique depends on factors such as whether the ground treated has sand or pebbles and whether the fertiliser is water soluble or applied in pellet or liquid form.
Powered by
Translate

No comments:
Post a Comment